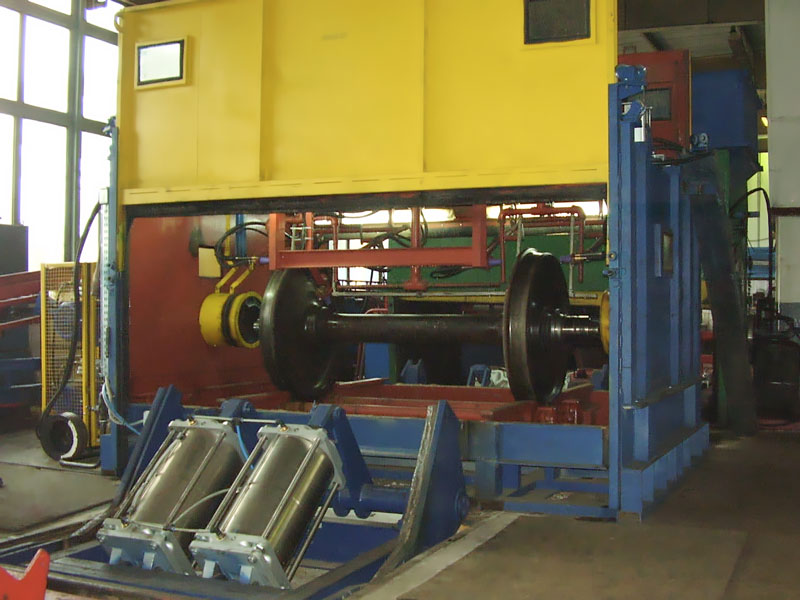
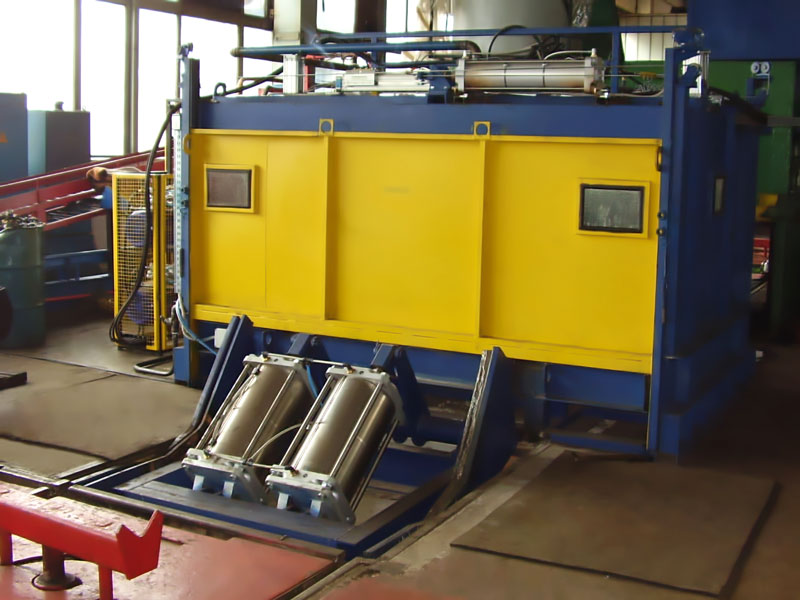
The automated wheel set cleaning and washing station is designed for pressure washing of freight railcar wheelsets with a heated cleaning solution, followed by rinsing with heated water and drying.
The automated station is a closed-cycle, sealed chamber of the tunnel type. The treatment is carried out by applying a heated cleaning solution under pressure to the dirty surfaces of the wheelset. Rotation around its axis ensures high-quality cleaning of the wheelset from all sides.
The automated station comprises:
- a conveyor mechanism for moving wheel sets;
- wheel set feeder (inlet and outlet);
- nozzle systems adapted to the geometry of the wheelset;
- washing solution filtration system;
- hydraulic system with pumps and a washing circuit for supplying solutions;
- tank 1 for washing;
- tank 2 for rinsing;
- connecting pipes to the vapour extraction system;
- oil and grease trap;
- control system;
- emergency stop system.
The chamber body of the automated station is made of stainless steel and insulated with thermal panels. A thermal insulation layer between the outer and inner coatings ensures good heat and sound insulation. The washing liquid heating tank and the rinse water tank are located separately next to the washer. The tanks and pipework are also made of stainless steel. There is a drip tray under the washing chamber for collecting the washing solution during the washing process. Each tank is equipped with a digital thermostat with a selectable solution heating temperature of 90-95 ᵒC. The wheelset is washed by an integrated spray device using a special nozzle system adapted to the geometry of the wheelset. Water is pumped from the sump into the tank by a drainage pump, and then the cleaned liquid is pumped from the tank to the washing circuits by a pressure pump. The wheelset rotates to ensure that the wheelset is cleaned completely. The washing chamber is equipped with steam extraction nozzles, minimum/maximum solution level control and automatic water refill. The door lift drive is located on the roof of the chamber.
The built-in time control of the washing cycle automatically maintains the workflow of cleaning the components. The doors of the washing chamber are hermetically sealed, allowing for a safe rinsing and cleaning process.
The control system ensures automatic feeding of the wheelset into the washing chamber, its washing and rinsing with water, drying of the wheelset, and then moving the washed and dried wheelset out of the washing chamber. The control system ensures that each mechanism of the machine is controlled in the adjustment mode after assembly, during maintenance, repair and other essential occasions.
Operation principle
The dirty wheelset is fed into the washing chamber via the feeder and placed on the rollers of the rotation mechanism. When the WASH button is pressed on the control panel, the machine mechanisms start working automatically. The chamber door closes and the washing process begins. When the washing process is complete, the wheelset is rinsed with water. The duration of washing, rinsing and compressed air blowing is set by the programme from the control panel. After the set time has elapsed, all electric motors are switched off and the wheelset rotation stops. The chamber door is opened, the wheelset rolls out of the chamber and stops at the feeder behind the chamber. The washing cycle is complete, the complex is ready to receive the next dirty wheelset.
Technical characteristics:
1. | Type | Sealed chamber of the tunnel type |
2. | Type of drive for feeding/extracting the wheelset | pneumatic |
3. | Drive for opening the door | electromechanical |
4. | Heating temperature of solutions | 90-95 ᵒC |
5. | Heating of the washing solution | heating elements |
6. | Power of washing pumps 1 tank | 11 kW |
7. | Pressure of washing pumps 1 tank | 7.5 bar |
8. | Power of washing pumps 2 tank | 4.4 kW |
9. | Pressure of washing pumps 2 tank | 5.6 bar |
10. | Total power consumption | 112 kW |
11. | Overall dimensions: | |
height with doors open | 3920 mm | |
width | 4800 mm | |
length | 6000 mm |