The line is designed for drying and deoiling of outer pipe surface, cleaning it from dirt, rust, oxides and other contaminations as well for covering anticorrosion insulation of 3 layers (adhesive substance, polyethylene).
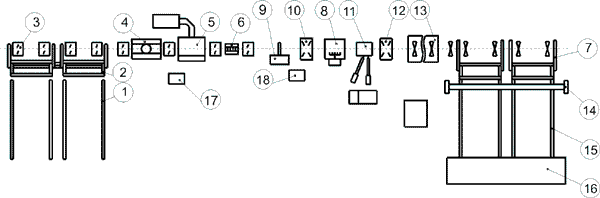
1. Roller conveyor | 8. Extruded polyethylene insulation unit |
2. Stower rack | 9. Roll-on system |
3. Remover | 10. Cooling system |
4. Pipe drying chamber | 11. Coating cutting device |
5. Shotblast unit | 12. Defectoscope |
6. Pipe heating unit | 13. Electrical equipment |
7. Underlayer coating chamber |
The insulation is a coating of 2,5 – 3,0 mm with extruded polyethylene based on solid adhesion underlayer – copolymer ethylene with vinyl acetate. The adhesion underlayer provide the layer with high adhesion on the steel pipe, the outer polyethylene layer gives necessary mechanical strength.
In comparison to the bitumen insulation, polymer insulator and others used now the coating with extruded polyethylene on solid adhesion underlayer as well the possible postprocess control in the plant conditions let achieve the higher figures of coating quality especially concerning outer mechanical impact resistance, high adhesion to the pipe surface, reduced water absorption and water resistance which provide the pipelines with long, failure-free service (40 to 50 years).
The insulation technology meets the State Standards.
The pipe drying chamber
The pipe drying chamber is intended for pipe preheating and drying. It is equipped with 4 gas burners and automatics to keep the operation of the line. Gas supply and smoke removal system are done by authorized companies and lay by the Customer.
The shotblast unit
The shotblast unit is intended for pipe cleaning till the 2nd purification efficiency acc. to GOST 9.402-80 (PSA2½ ISO 8501-2) and with roughness of 40-90 µm. It is equipped with shot feeding and recuperation systems which are integrated with dust removal device and air cleansing.
The pipe heating unit
The pipe heating unit is intended for pipe heating till adjusted temperature before polyethylene coating on pipe surfaces. The temperature range is of 150°С to + 220°С depending on the adhesion underlayer. It is equipped with 4 gas burners mounted at right and left chamber walls and with automatics to keep the operation of the line. The burners can work in pairs.
The equipment for extruded polyethylene coating
The underlayer coating chamber is intended for continuous conversion of granual glue compositions into a uniform melted substance and then to cover with it the cleaned pipe surface heated till the adjusted temperature. The unit consists of a worm press (extruder) equipped with a heat regulation block, electrical drives, control panels, a loader, a filter gate and a slit extrusion head.
The cooling systems
The cooling systems intended for water cooling of the outer polyethylene protective layer immediately after the coating process. The tunnel is a bath, a water tank, covered by the casing with removable walls. In the bath there are rollers of the roller conveyor and collectors with water nozzles directed toward the area closed to the lower pipe. In the casing there are collectors with water nozzles directed toward the area closed to the upper pipe. The collectors can be adjusted in the height.
The coating cutting device
The coating cutting device is intended for cutting of the coating at pipe connections and two circular cuts (to steel surface) in the distance of 100-150 mm from the pipe butt-ends.The cutting device is a carriage with 3 disc knives. The carriage is mounted on a horizontal guide. The approach and moving off of the knives is controlled manually. The middle knife of the carriage which is directed to the butt between the pipes fulfills the axial move of the carriage according to the pipe move velocity.
The electrical control unit
The electrical control unit consists of a metal cabinet with all the necessary electrical equipment for the safety operation according the valid standards. The control system is based on logical modules LOGO, Siemens. It has a high safe operation, low costs, small size, simple programming, mounting and maintenance.