Since 2016, Interpipe has been producing railway wheels and wheelsets for high-speed trains with higher added value. This type of product is in demand in the transportation infrastructure of European and American countries, which was the reason for the company to make large investments in launching several new production sites, including the creation of sites that ensure the application of operational and anticorrosion coatings on the manufactured railway wheels.
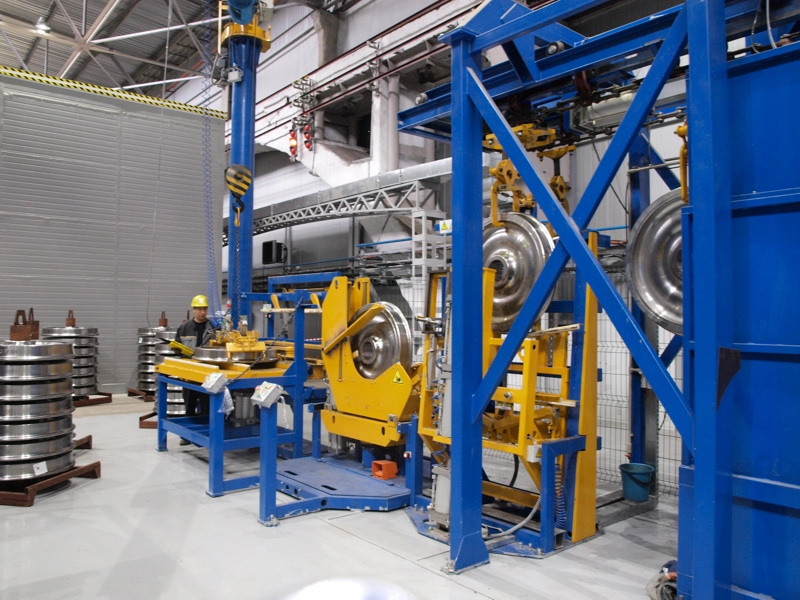
Designing and manufacturing of equipment for the areas being created for the application of operational and anticorrosion coatings on manufactured products was carried out by Research-and-Production Enterprise ‘TECHWAGONMASH’ (director A.N. Motorin, Kremenchuk).
As a result of this work, the specialists of the enterprise created the first in Ukraine semi-automatic line for the application of operational and anti-corrosion coatings on railway wheels. Even though the operation period of this line is rather short yet, it has already received positive feedback from the customer. The line provides the application of operational and anticorrosion coatings on the whole range of wheels produced by the customer company.
The equipment of the line was developed in full compliance with the technology prepared by the customer company “Interpipe”, for applying the most complex, in technological terms, operational coating Wilckens SEB 9303, which is an indicator of overheating of the wheel surface during operation. The signs of the wheel surface coating overheating (at t=220…230°C the coating changes colour and at t=250…300°C the coating blisters), serve as a signal to replace the wheelset.
The equipment created by TECHWAGONMASH ensures compliance with high requirements for surface preparation before coating, application of coating, and curing modes. This is one of the main advantages of the line equipment designed by TECHWAGONMASH.
Thus, the control system of the line equipment controls the processes of solutions feeding to the spray nozzles, maintenance of the set levels of water and solutions in the baths, their replenishment, protection of pumping units operation against dry start, water level overflows are ensured by level and temperature control sensors, thermostatic regulating valves, safety valves, and in the chambers of painting, coating normalisation, drying and cooling of the wheel surface – the necessary technological parameters are ensured by the operation of the temperature and air circulation sensors system. The quality of the coating applied on the line equipment fully meets the Customer’s requirements.
During the design and manufacture of equipment, we successfully solved the problem of using the designed line equipment for the application of certain types of water dispersion and organically soluble paint and varnish materials, which is a great advantage as it allows the company to respond flexibly to the needs of customers.
Composition and operation principle of the railway wheel surface coating line
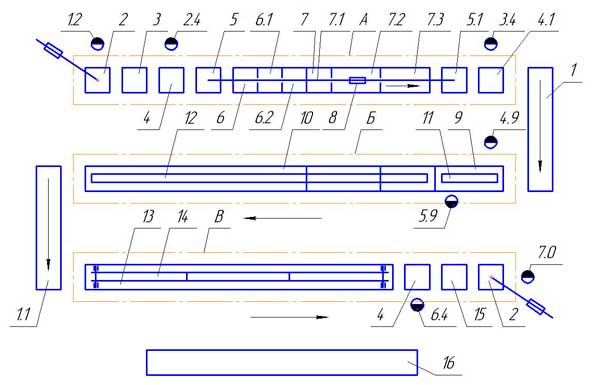
Composition and operation principle of the railway wheel surface coating line
The line consists of three functionally separate sections: A, Б, and B. Section‘A’ of the line include line loading equipment and surface preparation equipment for coating: manipulator (item 2), positioner (item 3), wheel surface incoming inspection station (item 4), lifts (item 5 and 5.1), surface washing and degreasing chambers (item. 6, item 6.1, item 6.2), wheel surface drying and cooling chambers (item 7), wheel surface preparation quality control station (item 4.1). Wheel transfer from position to position is carried out utilizing the transport system of the surface preparation line (item 8).
Section ‘Б’ of the line includes equipment for coating – painting chamber (item 9), equipment for coating normalisation and drying – normalisation chamber, active drying chambers (thermo-radiative-convective and convective) (item 10).
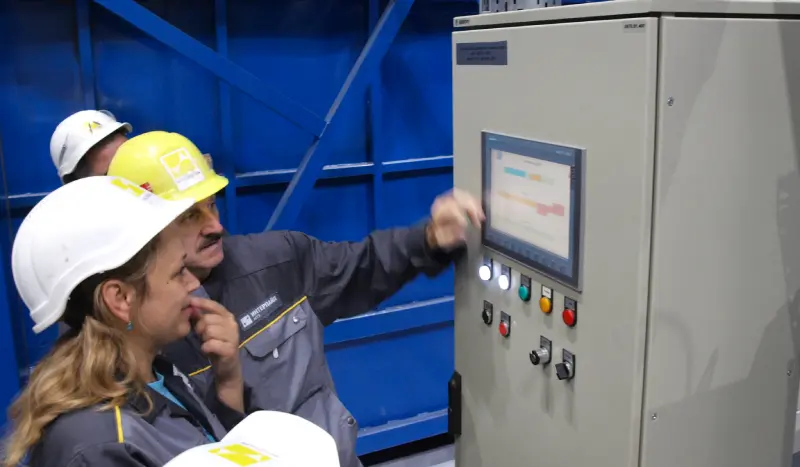
The wheel is transferred between positions in the painting chamber (item 11) and then into the drying chamber by the transport system of the active drying line (item 12). Section ‘В’ of the line includes the cooling chamber (item 13), wheel surface coating quality control station (item 4), and positioner (item 15). The transport system of the cooling chamber (item 14) moves the wheel in the chamber. The manipulator (item 2) removes wheels from the line and stacks them in cassettes.
The line has a common control system (item 16), and its functionally separate parts are equipped with control panels for performing work in the adjustment mode. The line is equipped with safety equipment and interlocks preventing unauthorised start-up of mechanisms, which could lead to equipment breakdowns or injury to operating personnel.
The semi-automatic line for the application of the operational coating on railway wheels works as follows:
Section «А» (wheel surface preparation before coating)
– wheels in containers in which they are stacked in several layers, with a common vertical axis, are transported by the shop’s electric forklift from the billet warehouse to the storage area of the line and placed on the storage area positions;
– then, the wheels are removed from the container by a console manipulator equipped with an automatic gripper and placed in the positioner of the loading zone of the line.
Console loading manipulator consists of an automatic gripper mounted on the console of a single-axis crane with a lifting and lowering mechanism.
After the wheel is placed in the positioner, its frame turns and sets the wheel in a vertical position. With the roller door of the degreasing chamber open, the pusher of the wheel positioner pushes the wheels into the wheel delivery chute, and through this chute, they are rolled into the washing and phosphating solution application chamber.
Then the wheel is successively moved to the wheel holding chambers under a layer of washing and phosphating solution, the wheel washing chambers with clean water, to the air blowing chamber, item 1.8, after degreasing, and finally to the wheel drying and cooling chambers.
The lower part of the chambers: application of washing and phosphating solution, item 1.4, wheels are kept under the layer of washing and phosphating solution, item 1.5, chambers for washing wheels with clean water, item 1.6, 1.7 after degreasing the wheels rest on the baths so that process liquids can be collected.
Section «Б» (coating, normalisation, and drying of the coating)
At the loading position of section ‘Б’ of the line, the wheels are transferred by the transport system, then transferred to the degreasing quality control position, and then through the passage to the painting chambers for masking of non-paintable surfaces and wheel painting. After the wheels are coated, the non-paintable surfaces are demasked and the wheels are transferred to normalisation chambers and thermo-radiative-convective and convective drying chambers.
Section «В» (coating curing and wheel cooling)
The wheels are then transferred by the transport system to the coating curing and cooling chambers. After cooling, the wheels are transported to the paint quality control position, and the wheel barcode labels are applied to the rims of the painted wheels that have passed the quality control test.
If the paint quality is adequate, the wheel is fed to the wheel positioner, which turns the wheel to the horizontal axis position. The wheel is removed from the wheel positioner by a cantilever manipulator with an automatic gripper, then it is transferred to the storage area and placed in a container located in the storage area for further transport of containers with wheels by a workshop overhead travelling crane to the finished product warehouse. The ventilation system ducts are located at the top of the line, above the chambers.
Additional characteristics of the railway wheel surface coating line
The line is operated by 8 persons – 7 operators and a foreman. Two operators operate the manipulator (item 1.2; 7.0), three workers are in the inspection area (item 2.4; 3.4; 6.4) and two painters paint the wheels (item 4.9; 5.9).
Wheels that pass through the line can be from 700 to 1350 mm in diameter. The capacity of the line is 15 wheels per hour.